7 Reasons Why Cnc Plasma Cutters Are Essential for Modern Manufacturing Success
In today's fast-paced manufacturing landscape, operational efficiency and precision are paramount. CNC plasma cutters emerge as a crucial technology in meeting these demands, offering versatility and speed in metal fabrication. According to a report from MarketsandMarkets, the global CNC plasma cutting machine market is projected to grow from $3.08 billion in 2021 to $4.68 billion by 2026, reflecting a compound annual growth rate (CAGR) of 8.5%. This growing acceptance of CNC plasma cutters demonstrates their essential role in enhancing productivity and reducing operational costs, making them a formidable tool in modern manufacturing.
Moreover, the adoption of CNC plasma cutters is transforming traditional manufacturing practices. A study by ResearchAndMarkets highlights that advanced CNC machines, including plasma cutters, improve cutting accuracy by over 30% compared to manual methods. This level of precision not only minimizes material waste but also decreases project turnaround times. As manufacturers seek to remain competitive in a rapidly evolving market, the integration of CNC plasma cutters into their production processes is no longer just an option but a necessity for sustained success.
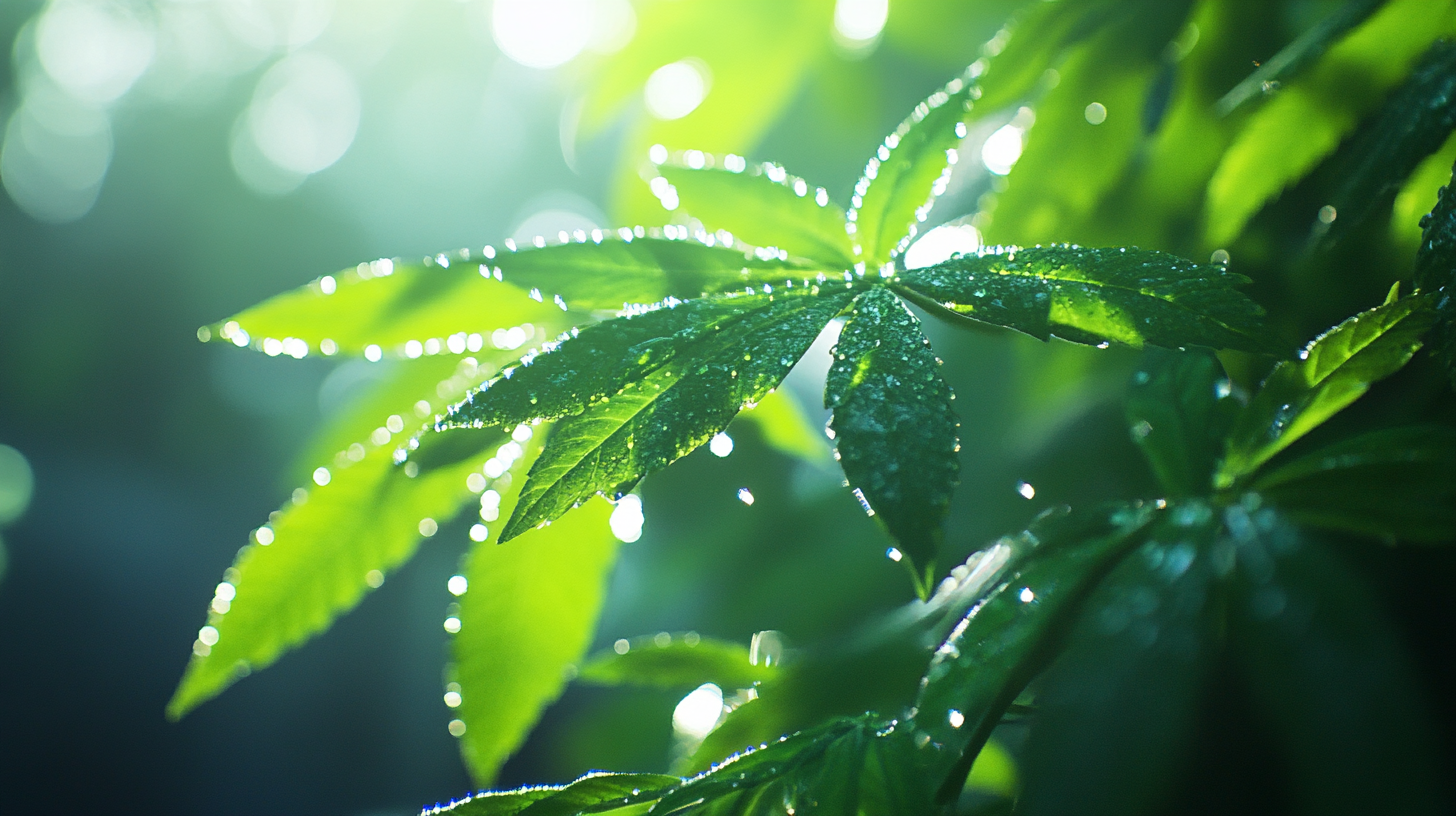
The Precision Advantage: How CNC Plasma Cutters Enhance Cutting Accuracy
CNC plasma cutters have revolutionized the manufacturing landscape, bringing a level of precision that was previously unattainable. The introduction of these advanced cutting tools has enabled manufacturers to enhance their cutting accuracy significantly. As reported, the global CNC plasma cutting machines market was valued at approximately USD 673.2 million in 2024 and is projected to grow at a compound annual growth rate (CAGR) of over 5.1% from 2025 to 2034. This upward trajectory highlights the increasing reliance on precision cutting technologies in various industries. The precision advantage of CNC plasma cutters lies in their ability to produce intricate designs with high repeatability. Unlike traditional cutting methods, which can be subject to human error, CNC plasma cutting machines operate on computer numerical control, ensuring that every cut is executed with impeccable accuracy. According to recent market analyses, the CNC segment alone accounted for over USD 419.1 million in 2023, underscoring its critical role in modern manufacturing processes. Moreover, as industries continue to embrace automation, the integration of AI in CNC systems is poised to further enhance cutting accuracy and efficiency. This evolution allows for real-time adjustments during the cutting process, ensuring optimal results, especially when dealing with complex geometries. The combination of these technologies is setting the stage for the future of precision manufacturing, making CNC plasma cutters not just useful, but essential for success in the modern manufacturing arena.
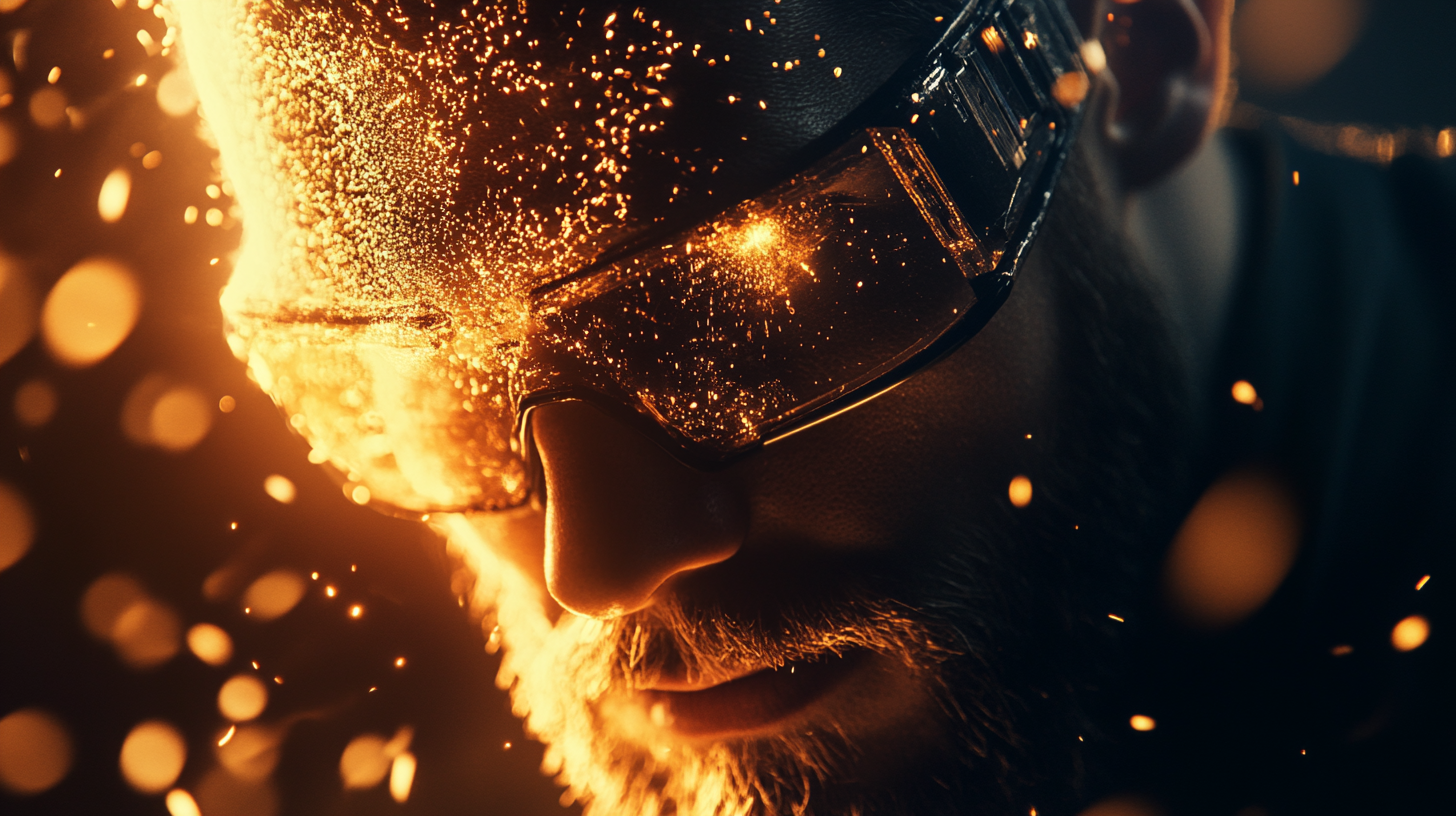
Boosting Productivity: The Role of CNC Plasma Cutters in Efficient Workflows
CNC plasma cutters play a crucial role in modern manufacturing by enhancing efficiency and productivity in various workflows. With the ability to cut through thick materials with precision and speed, these machines streamline operations that were once labor-intensive and time-consuming. By automating the cutting process, manufacturers can significantly reduce the time required to produce components, allowing them to meet tight deadlines without compromising on quality.
Furthermore, CNC plasma cutters contribute to optimized resource management. With their advanced programming capabilities, businesses can minimize material waste during the cutting process. This not only leads to cost savings but also promotes sustainable practices in manufacturing. The ability to produce accurate cuts ensures that materials are utilized to their fullest potential, making processes more eco-friendly and economically viable.
In addition to improving productivity, CNC plasma cutters enhance workspace safety. By automating the cutting tasks, these machines reduce the risk of operator injury associated with manual cutting tools. Workers can focus on overseeing operations rather than directly handling dangerous equipment, which fosters a safer environment. By integrating CNC plasma cutting technology into their workflows, manufacturers can improve overall efficiency while promoting a culture of safety and innovation.
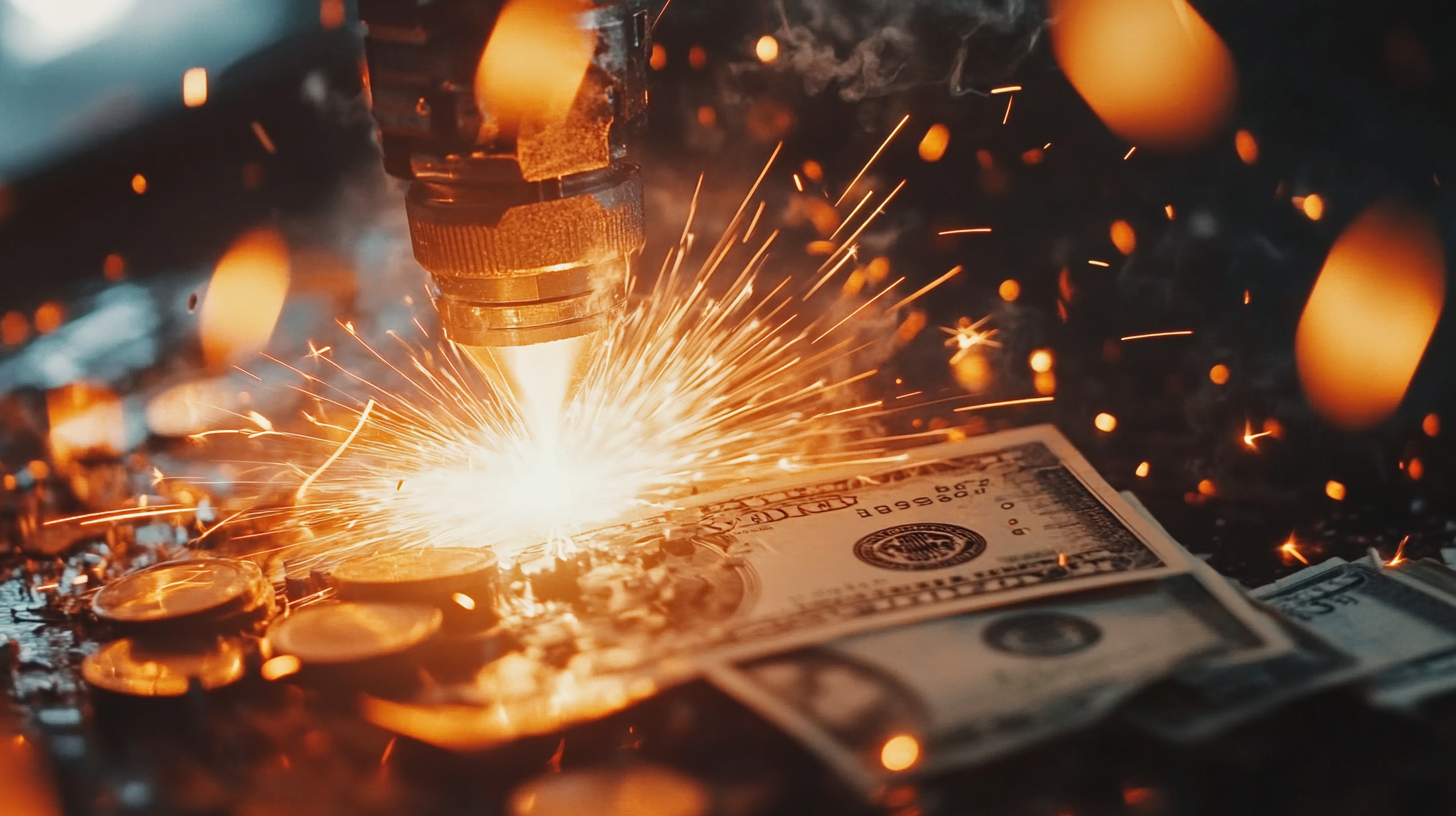
Versatility in Materials: Why CNC Plasma Cutters Are Suitable for Various Industries
CNC plasma cutters have revolutionized modern manufacturing by providing unrivaled versatility in material processing. From metal fabrication to automotive industries, the ability to efficiently cut through various materials makes plasma cutting technology an essential tool. The market for CNC plasma cutting machines is expected to experience substantial growth, driven by their applications in diverse sectors. According to recent analysis, the demand for CNC/automated machines is burgeoning, highlighting the advantages they offer over traditional cutting methods.
One of the primary reasons for the widespread adoption of CNC plasma cutters is their compatibility with multiple materials, including steel, aluminum, and copper. This versatility allows manufacturers to seamlessly integrate plasma cutting into their production lines, ensuring that they can adapt to changing customer needs and industry trends. A report indicates that the overall laser cutting machine market is projected to grow at a CAGR of 6.5% from 2025 to 2034, underlining the increasing preference for advanced cutting technologies in industrial applications.
Moreover, the efficiency of CNC plasma cutting compared to manual methods cannot be overstated. Automated systems reduce waste and enhance precision, which is crucial for maintaining competitiveness in a market that demands high-quality outputs. The precision and adaptability of CNC machines not only streamline the manufacturing process but also encourage innovation, enabling businesses to explore new design possibilities. As industries continue to evolve, the role of CNC plasma cutters in modern manufacturing will undoubtedly expand, solidifying their importance across various fields.
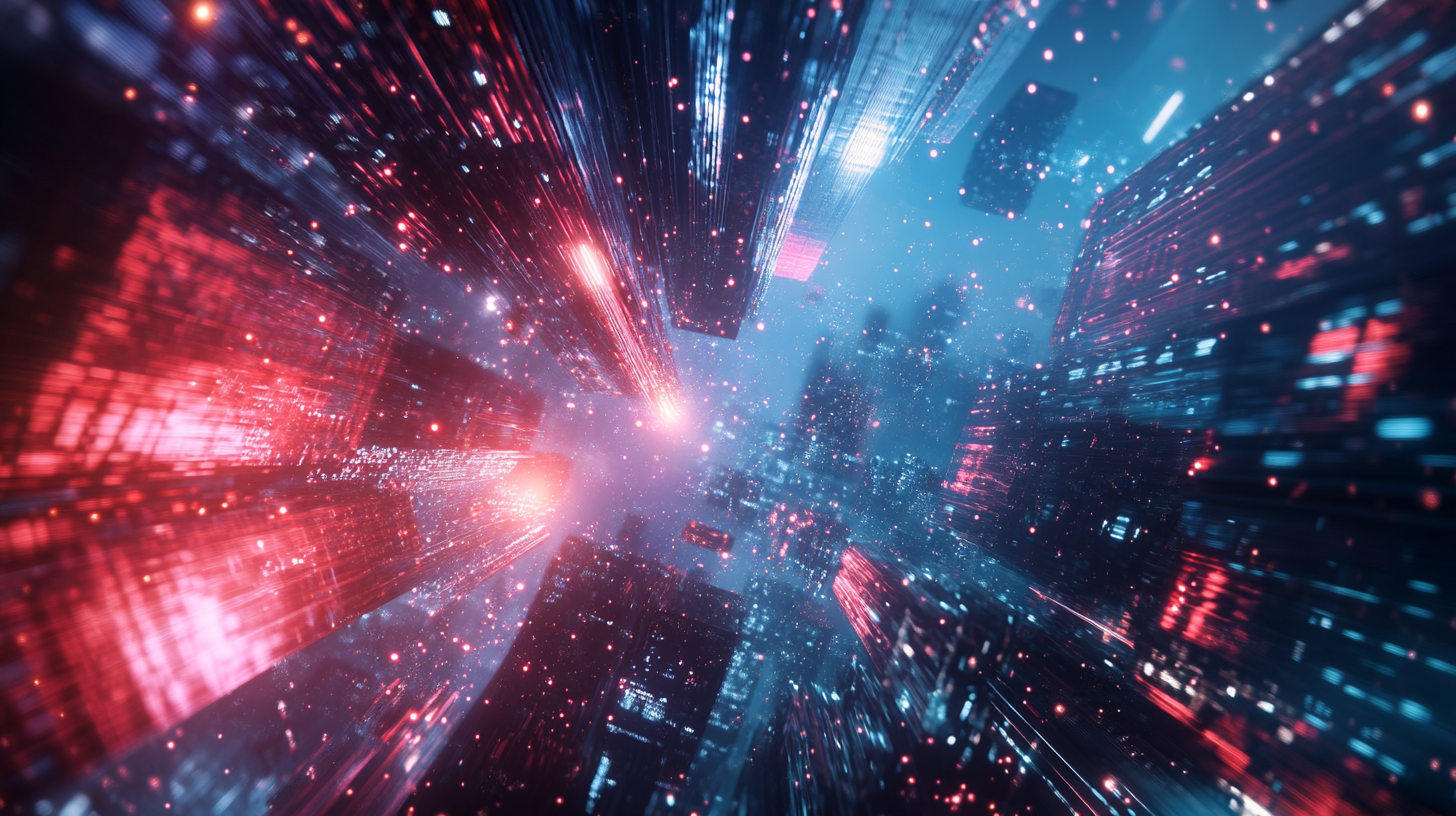
Cost-Effectiveness: Reducing Waste and Operational Costs with CNC Plasma Cutting
In the realm of modern manufacturing, cost-effectiveness has become a pressing need as businesses strive to remain competitive. CNC plasma cutting, with its unique ability to minimize material waste, plays a vital role in achieving this goal. One of the remarkable advantages of CNC plasma cutters is their compatibility with automatic nesting software. This innovative technology allows manufacturers to optimize the layout of parts on sheets of material, ensuring minimal scrap and thus significantly reducing operational costs.
The intelligent features of CNC plasma cutting systems facilitate precise cutting paths and efficient utilization of resources. By effectively minimizing material losses, companies not only save on raw materials but also benefit from lower overall production costs. With the ability to adapt to various materials and designs, CNC plasma cutters provide flexibility that traditional cutting methods cannot offer. As manufacturers increasingly adopt these advanced solutions, they find themselves well-positioned to enhance productivity while maintaining high-quality standards in their products.
Moreover, the widespread implementation of advanced machining technologies, including CNC plasma cutting, signifies a transformative shift within the manufacturing industry. Embracing these modern tools equips businesses to meet evolving market demands and stay ahead of competitors. The streamlined operations enabled by these systems not only drive down costs but also pave the way for innovative design possibilities, ultimately contributing to long-term success in manufacturing.
Innovation in Design: How CNC Plasma Cutters Enable Complex Geometric Shapes
CNC plasma cutters have revolutionized the landscape of modern manufacturing by enabling the creation of intricate and complex geometric shapes that were once thought to be unattainable. These machines harness the power of high-temperature plasma to cut through a variety of metals with precision and speed, allowing designers and engineers to bring their most ambitious ideas to life. As a result, industries ranging from automotive to aerospace benefit from the versatility and accuracy that CNC plasma cutters offer.
The key innovation behind CNC plasma cutting lies in its ability to execute detailed designs with minimal manual intervention. Advanced computer numerically controlled (CNC) systems allow for the programming of highly precise cutting paths, ensuring that every curve and edge is replicated flawlessly. This level of control not only reduces material wastage but also speeds up the production process, enabling manufacturers to respond quickly to market demands while maintaining high standards of quality.
Moreover, CNC plasma cutters can handle a variety of materials, including mild steel, stainless steel, and aluminum, making them indispensable tools across multiple sectors. The ability to create complex shapes also opens new possibilities for product design, leading to more innovative and efficient solutions. From decorative elements in architecture to functional components in machinery, the capabilities of CNC plasma cutters continue to push the boundaries of what can be achieved in manufacturing design, making them essential for companies that aspire to achieve success in a competitive landscape.