Unlocking Precision and Efficiency with Best Cnc Cutting Table Technical Specifications and Setup Guide
In the world of manufacturing and fabrication, precision and efficiency are paramount, and the Cnc Cutting Table emerges as an essential tool to achieve these goals. This advanced technology not only enhances the accuracy of cutting various materials but also streamlines the overall production process. In this blog, we will delve into the best technical specifications of Cnc Cutting Tables and provide a comprehensive setup guide to help users optimize their operations. Whether you are a seasoned professional or a beginner looking to integrate this cutting-edge equipment into your workflow, understanding the intricacies of Cnc Cutting Tables is crucial. Join us as we unlock the potential of this powerful tool and explore the features that can significantly elevate your manufacturing capabilities.
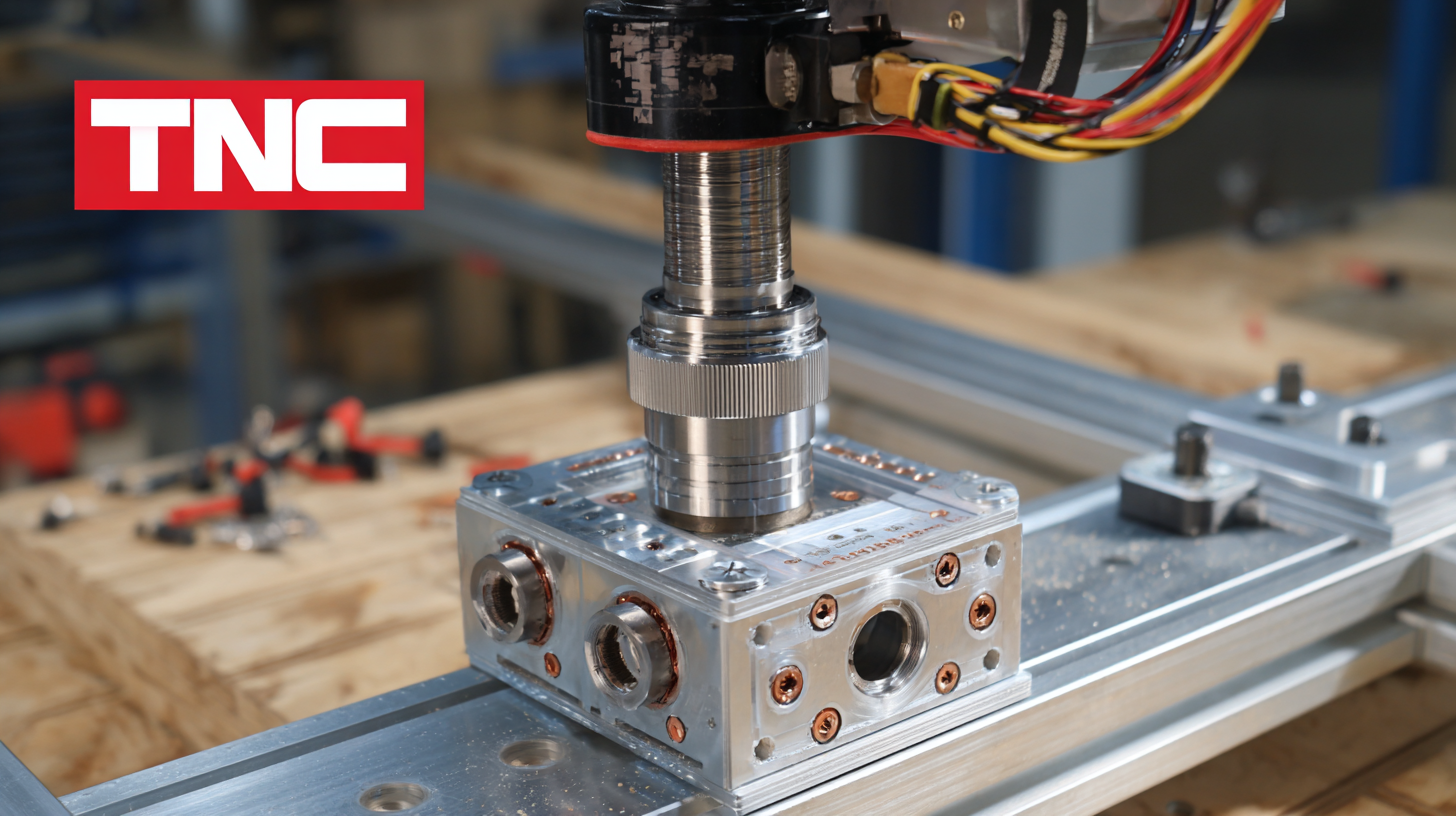
Optimizing CNC Cutting Table Specifications for Maximum Efficiency and Precision
In the realm of CNC machining, the focus on optimizing specifications is crucial for enhancing both precision and efficiency. With the global 5-axis CNC machining centers market poised to grow by USD 792.5 million from 2024 to 2028, driven largely by advancements in self-optimized machine cutting and artificial intelligence, the integration of innovative technologies is becoming increasingly vital. These improvements can significantly reduce machining errors, such as deviations in cutter contacting point trajectories, by employing advanced algorithms like the SA-PSO fusion technique to streamline machining paths for complex parts.
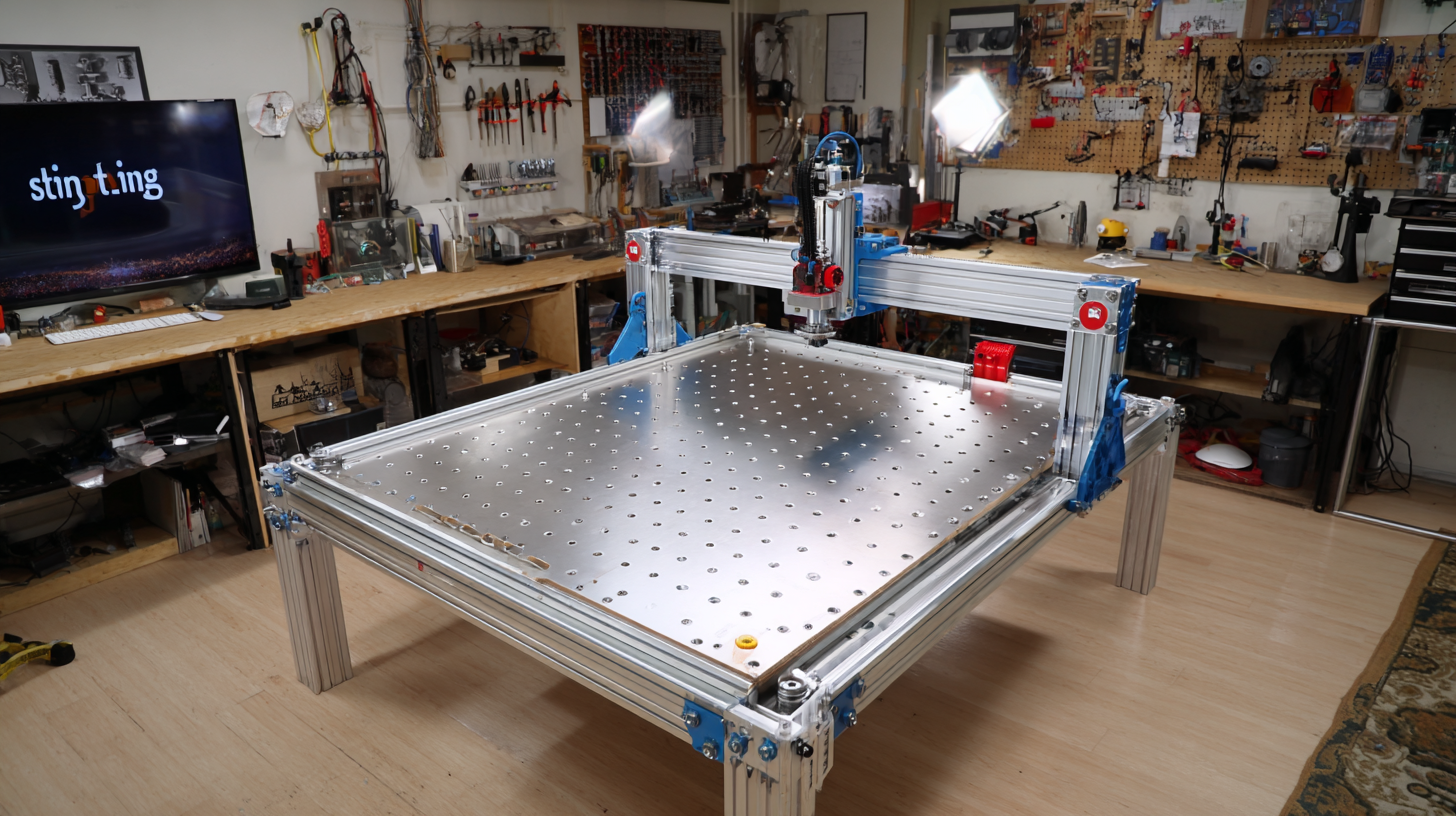
The influence of AI on CNC technology cannot be overstated. As industries adopt AI-driven solutions, manufacturers are not only enhancing cutting efficiencies but also minimizing waste and lowering production costs. Reports indicate that these AI initiatives are revolutionizing machining operations, allowing for more adaptive and intelligent manufacturing processes. By focusing on optimizing CNC cutting table specifications, manufacturers can achieve maximum operational efficiency and precision, setting a new standard for excellence in mechanical part production.
Essential Features of High-Performance CNC Cutting Tables for Complex Projects
In the world of advanced manufacturing, CNC cutting tables play a pivotal role in executing complex projects with remarkable precision and efficiency. Essential features of high-performance CNC cutting tables include robust cutting capabilities, rapid processing speeds, and the adaptability to work with various materials. These attributes enable manufacturers to address intricate designs and specifications, ultimately driving innovation in production lines.
The recent launch of a flame cutting project exemplifies how upgraded technology can enhance operational efficiency. By integrating a specialized CNC cutting table in their operations, manufacturers can alleviate the burdens of traditional cutting methods, streamline workflows, and increase output rates. This shift not only accelerates production cycles but also ensures that the quality of cut materials meets the stringent requirements of modern applications. The evolution of CNC cutting technology signifies a leap forward, allowing businesses to tackle complex projects with confidence and agility.
Performance Comparison of CNC Cutting Tables
The Impact of Material Types on CNC Cutting Table Setup and Functionality
The impact of material types on CNC cutting table setup and functionality is significant, as different materials require distinct considerations for optimal processing. For instance, the laser processing market highlights various laser types, including CO2 and fiber lasers, each with specific advantages depending on the material being cut. Fiber lasers are typically preferred for metals due to their efficiency and precision, while CO2 lasers excel in cutting softer materials like plastics and woods. As industries increasingly adopt advanced cutting technologies, understanding the properties of materials can directly influence the effectiveness of production processes.
Additionally, recent findings indicate that cutting speed greatly affects surface roughness, especially in low-carbon steels. Research shows a staggering 90.08% difference between theoretical and experimental surface roughness values at a cutting speed of 226.19 m/min. This discrepancy underscores the importance of tailoring the CNC cutting table setup to the material and cutting speed used. By aligning these factors with the appropriate laser type, manufacturers can enhance the quality of finished products, reduce waste, and improve overall throughput in manufacturing operations.
Integrating Advanced Technology in CNC Cutting Tables: A Data-Driven Approach
In recent years, the integration of advanced technology in CNC cutting tables has revolutionized manufacturing processes. Recent industry reports indicate that businesses using modern CNC technology can achieve precision levels of up to 0.001 inches, significantly reducing material waste and enhancing productivity. This data-driven approach not only optimizes the accuracy of cuts but also allows for the efficient management of resources, ultimately leading to cost savings and improved profitability.
To maximize the benefits of these high-performance CNC cutting tables, it’s crucial to ensure proper setup and calibration. Here are some tips: First, regularly update the software to leverage the latest technological advancements and features. Second, make use of predictive maintenance strategies, which can reduce downtime by up to 30%, according to a study by the Manufacturing Technology Association. Lastly, training your staff on advanced machine operation techniques can enhance operational efficiency, resulting in up to a 20% increase in output.
Implementing a data-driven strategy for monitoring performance metrics is essential. Utilize real-time analytics to track cutting quality and machine performance. This approach not only enables immediate troubleshooting but also informs future buying decisions for cutting materials and machinery upgrades. By harnessing the power of technology and data, businesses can unlock unprecedented precision and efficiency in their CNC cutting operations.
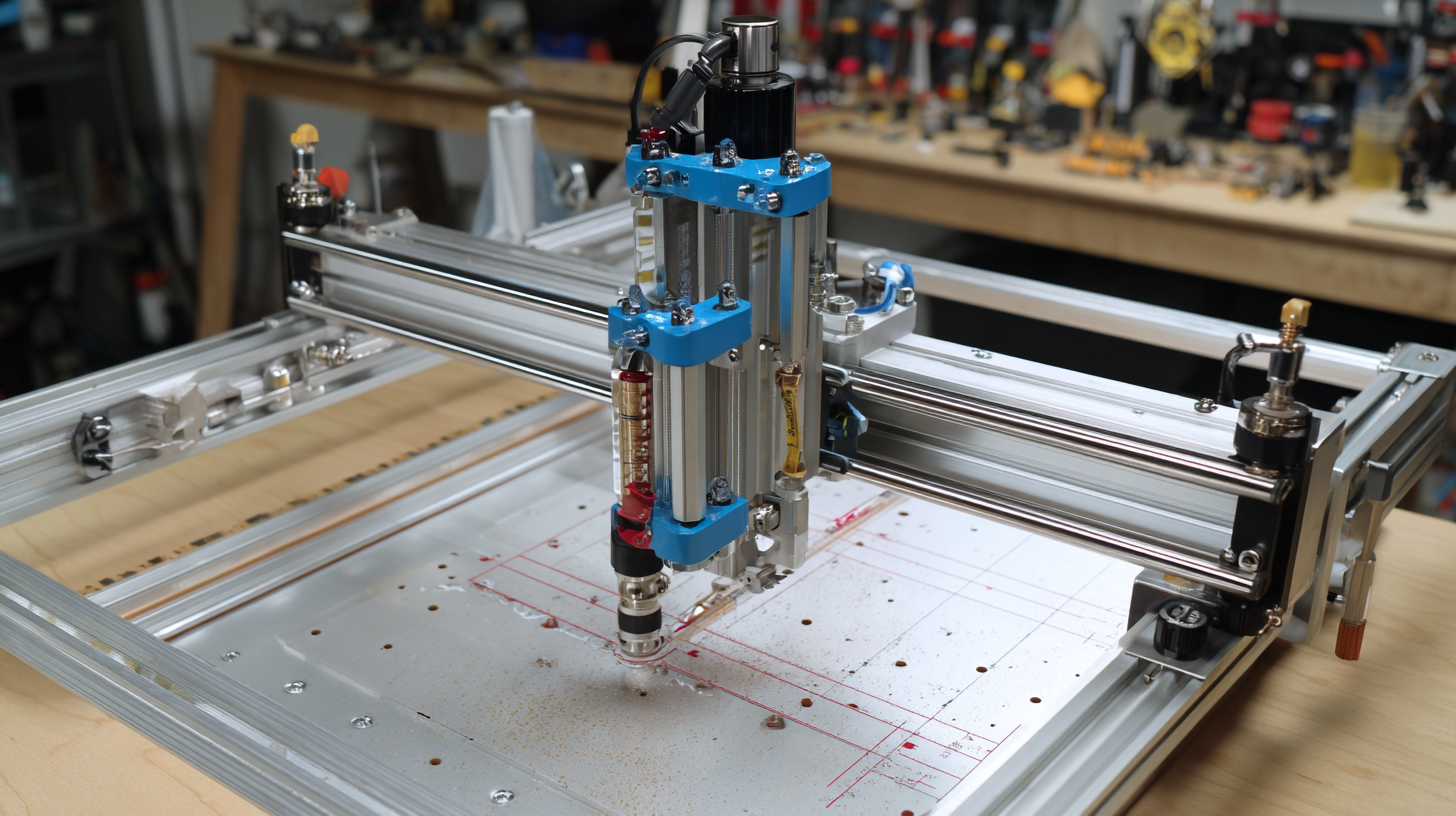
Best Practices for CNC Cutting Table Maintenance to Ensure Longevity and Performance
Maintaining a CNC cutting table is crucial to ensure its longevity and optimal performance. According to a report by the Association for Manufacturing Technology, regular maintenance can increase machine life by up to 25% and reduce downtime by as much as 50%. Implementing best practices such as daily inspections, proper cleaning, and lubrication not only enhances efficiency but also guarantees precision in cutting operations. Operators should consider scheduling weekly checks to ensure alignment and calibration, which could improve cutting accuracy by 15-20%, as indicated by a recent survey conducted by Modern Machine Shop.
Furthermore, it is essential to adhere to manufacturer guidelines for maintenance intervals. Research by the National Tooling and Machining Association suggests that machines that undergo routine maintenance display substantial improvements in performance metrics, including speed and cutting quality. Implementing a structured maintenance schedule can help identify wear and tear before they escalate into more significant issues, potentially saving thousands in repair costs. By making a concerted effort to prioritize the care of CNC cutting tables, businesses can significantly bolster their production capabilities while ensuring high-quality results with each cut.