Ultimate Guide to Choosing the Right Cnc Tube Cutter for Your Industry Needs
In today’s manufacturing landscape, the precision of cutting technologies has become a pivotal factor in ensuring the efficiency and quality of production processes. The demand for high-quality CNC machining has seen steady growth, with a recent report from MarketsandMarkets predicting that the CNC machine market is expected to reach $117.93 billion by 2026, growing at a CAGR of 6.3% from 2021. Within this expanse of CNC machines, the CNC tube cutter has emerged as a crucial tool for various industries, from automotive to aerospace, providing the accuracy necessary to meet stringent specifications.
Selecting the right CNC tube cutter is essential for optimizing operational efficiency and minimizing material waste. According to a survey conducted by IBISWorld, the metal cutting industry alone is projected to generate over $30 billion in revenue in the coming years. With advancements in technology and the rising complexity of tube designs, businesses must navigate a plethora of options to find a CNC tube cutter that aligns with their specific industry needs. This ultimate guide aims to illuminate the essential factors to consider when choosing a CNC tube cutter, ensuring that your investment translates into superior performance and productivity.
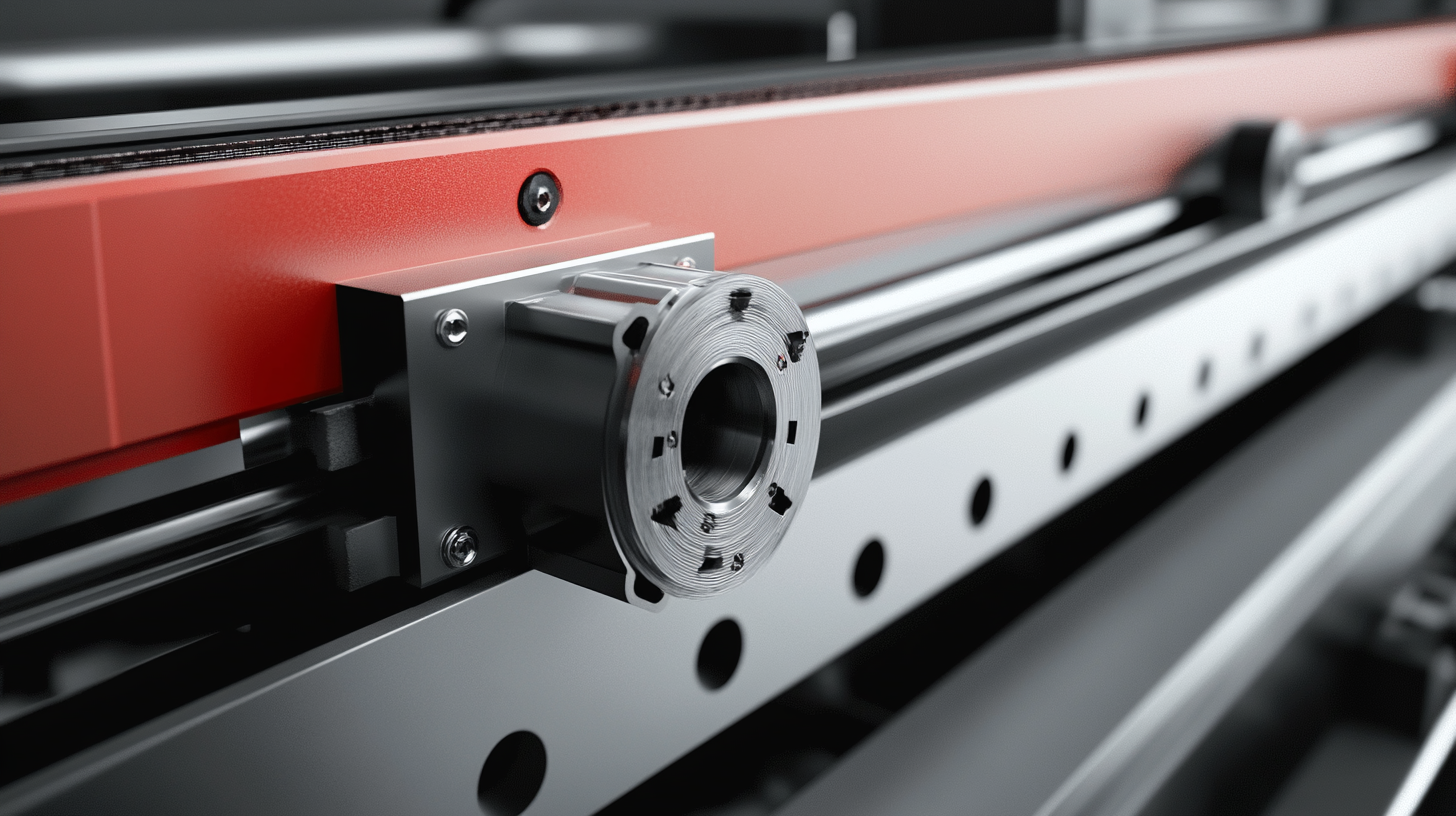
Key Factors to Consider When Selecting a CNC Tube Cutter for Your Industry
When selecting a CNC tube cutter for your industry needs, several key factors should be carefully considered to ensure optimal functionality and efficiency. First and foremost, the material of the tubes you will be cutting plays a significant role in determining the required cutter specifications. Different materials, such as stainless steel, aluminum, or copper, have varying properties that affect cutting speed and tool wear. Understanding the characteristics of these materials will guide you towards choosing a cutter that is durable and effective for your specific applications.
Another essential factor is the tube diameter and wall thickness. CNC tube cutters are available in various sizes and capabilities, and selecting one that aligns with the dimensions of your tubes is crucial. A cutter that can accommodate a wider range of tube sizes offers you flexibility in your operations, reducing the need for multiple machines and streamlining your workflow. Additionally, consider the complexity of the cuts required—whether you need simple straight cuts or intricate shapes—as this will influence your choice of technology, including laser, plasma, or rotary cutting methods.
Lastly, the level of automation and integration with existing systems is a vital consideration. The right CNC tube cutter should not only be compatible with your current machinery but also enhance productivity through features like automated loading, unloading, and real-time monitoring. Investing in advanced automation can lead to reduced labor costs and increased precision, making your operations more competitive in the industry.
Key Factor | Description | Importance | Recommendation |
---|---|---|---|
Material Compatibility | Ensure the cutter works with the specific tube materials in your industry. | High | Select a cutter designed for those materials. |
Cutting Precision | Look for the tolerance and accuracy of cuts needed for your applications. | Critical | Choose a model with high precision features. |
Speed & Efficiency | Consider cycle times and throughput requirements for your production. | High | Opt for equipment that balances speed with quality. |
Ease of Use | Assess the user interface and programming requirements. | Moderate | Look for intuitive controls and good support. |
Maintenance & Support | Evaluate maintenance needs and availability of technical support. | High | Select brands known for customer service and reliability. |
Types of CNC Tube Cutters and Their Specific Applications
When it comes to selecting the right CNC tube cutter for specific industrial applications, understanding the various types available on the market is crucial. CNC tube cutters can generally be categorized into two main types: laser tube cutters and plasma tube cutters. Each type possesses distinct advantages that cater to different materials and project requirements. According to a 2022 market research report by Research and Markets, the CNC tube cutting market is projected to grow at a CAGR of 6.5% from 2023 to 2030, indicating the increasing demand for precise cutting technology.
Laser tube cutters are known for their exceptional precision and ability to handle a variety of materials, including stainless steel, aluminum, and even non-ferrous metals. Their ability to produce clean, burr-free edges with minimal heat distortion makes them ideal for the aerospace and automotive industries, where precision is paramount. A study by TechsConfirm indicates that 78% of manufacturers in the aerospace sector prefer laser cutting for its efficiency and accuracy.
On the other hand, plasma tube cutters are often chosen for their speed and effectiveness in cutting thicker materials. They are particularly suited for industries such as construction and shipbuilding, where speed and cost-effectiveness are essential. According to the North American Industry Classification System (NAICS), approximately 60% of shipbuilders utilize plasma cutting technology for its ability to handle high-volume material with lower operational costs. Understanding these specific applications can help businesses make informed decisions about which CNC tube cutter best meets their manufacturing needs.
Ultimate Guide to CNC Tube Cutters
This chart illustrates different types of CNC tube cutters and their specific applications across various industries, showcasing the number of units sold in the last year.
Understanding Material Compatibility for Optimal Cutting Performance
When selecting a CNC tube cutter, understanding material compatibility is a pivotal aspect that can greatly influence cutting performance and operational efficiency. Different materials exhibit varied behaviors under cutting conditions. For instance, according to a market research report by Mordor Intelligence, the CNC machine tools market is projected to reach $100 billion by 2025, with significant growth driven by the demand for precision cutting in industries like automotive and aerospace. This demand stresses the importance of choosing the right cutter for specific materials such as steel, aluminum, or exotic alloys.
Aluminum, known for its lightweight and corrosion-resistant properties, may require a CNC tube cutter with specific features to prevent burrs and ensure a clean edge. The American Welding Society reports that improper cutting can lead to a costly increase in scrap material, which directly affects production costs. In contrast, cutting materials like stainless steel necessitates a robust cutter capable of withstanding higher temperatures and pressures without degrading performance. The selection process must therefore consider not just the materials but also the intended application, as choosing an incompatible cutter can lead to inefficiencies.
Furthermore, advancements in cutting technologies have introduced options that accommodate a diverse range of materials. Reports from industry analysts reveal that laser cutting has increased in popularity due to its precision and ability to handle sensitive materials without the risk of heat distortion. Understanding the unique properties of each material, along with the specifications of your CNC tube cutter, can enhance productivity and significantly reduce operational challenges, ensuring that your equipment and processes remain aligned with the strategic goals of your industry.
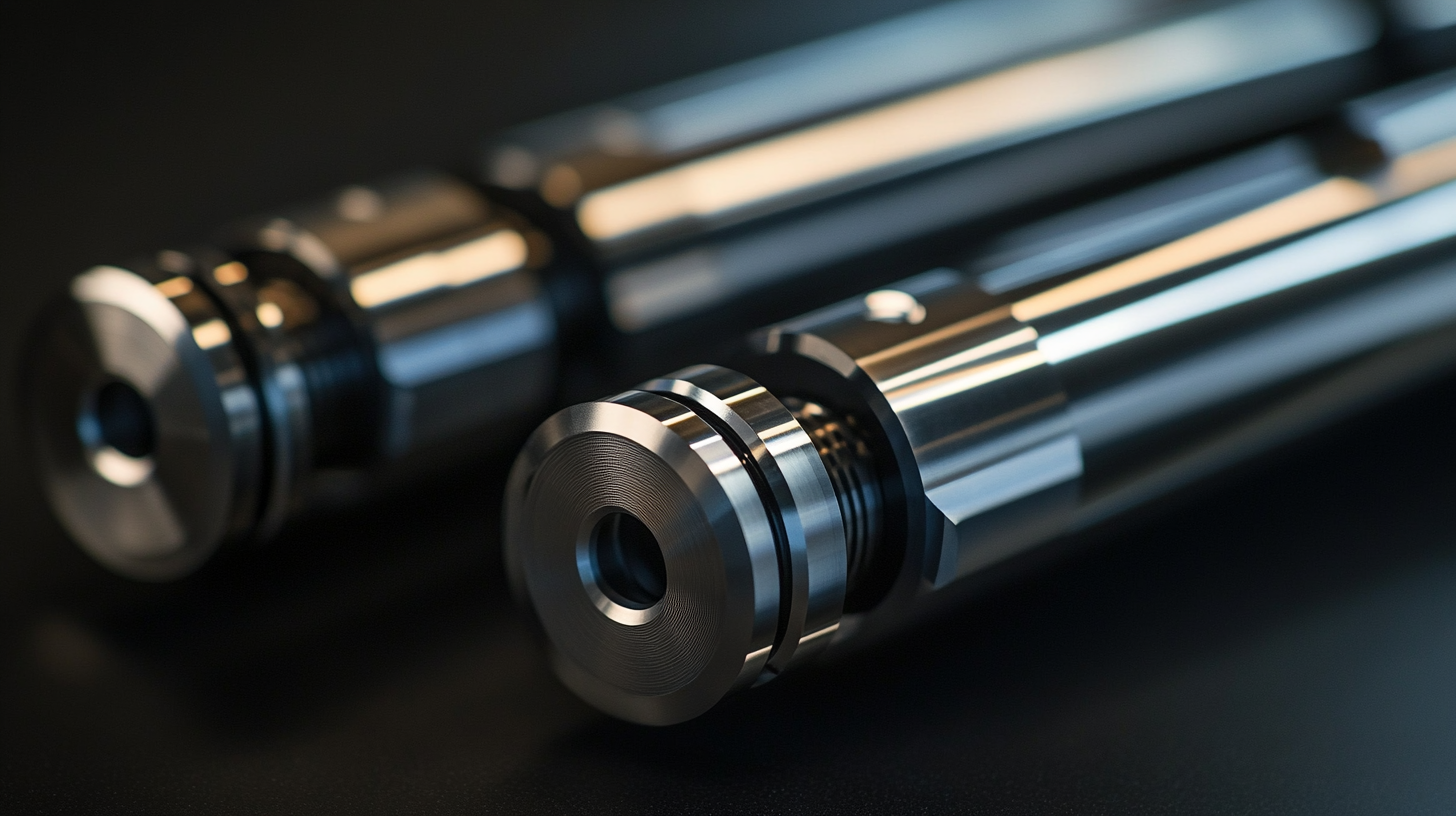
Evaluating the Cost-Effectiveness of CNC Tube Cutters: What You Need to Know
When evaluating the cost-effectiveness of CNC tube cutters, a thorough understanding of the long-term savings they provide is essential. According to a report by the Fabricators & Manufacturers Association, employing CNC technology can reduce production time by up to 50% compared to traditional methods. This significant time-saving translates directly into lower labor costs and increased throughput, making CNC tube cutters highly attractive for many manufacturers.
Moreover, the initial investment in CNC tube cutting technology can yield substantial returns. A market analysis from IBISWorld reveals that precision cutting machines can enhance material usage efficiency by as much as 20%, minimizing waste and optimizing raw material spending. This aspect becomes particularly significant in industries like automotive and aerospace, where material costs are substantial. Therefore, choosing the right CNC tube cutter not only impacts immediate productivity but also contributes to long-term financial sustainability.
Additionally, maintenance costs play a crucial role in assessing the cost-effectiveness of CNC tube cutters. A recent study from the National Tooling and Machining Association emphasized that modern CNC machines require less frequent servicing and have longer lifespans than their manual counterparts, leading to a decrease in overall maintenance expenses. Thus, businesses that invest in high-quality CNC tube cutters often find that the reduction in long-term upkeep significantly offsets the original purchasing cost, ultimately enhancing profitability.
In conclusion, by carefully evaluating the cost-effectiveness of CNC tube cutters, industries can ensure they make strategic investments that support efficiency, reduce waste, and bolster their bottom line.
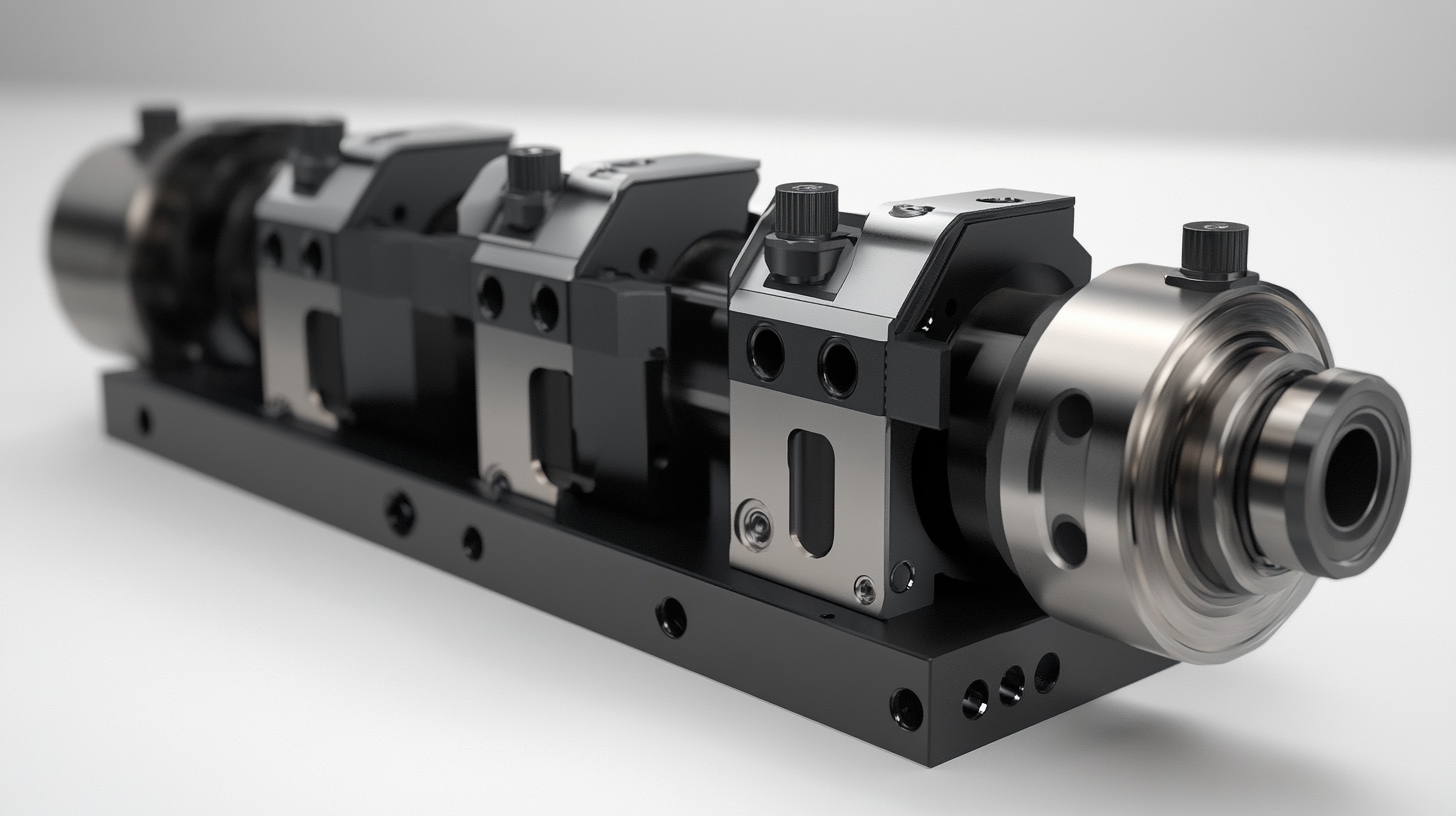
Maintenance Tips for Enhancing the Longevity of Your CNC Tube Cutter
Maintaining the longevity of your CNC tube cutter is essential not just for efficiency, but also for safeguarding your investment. Studies indicate that regular maintenance can increase the lifespan of CNC machines by up to 50%. One of the most critical maintenance tips is to keep the machine clean. Operators should regularly remove metal shavings and debris from the cutting area, as these contaminants can cause wear and tear on components over time. A clean workspace not only ensures optimal performance but also minimizes the risk of mechanical failure.
Another vital aspect of maintenance involves regular checks on the cutting tools themselves. According to the National Tooling and Machining Association, dull or damaged cutting tools can lead to a decrease in productivity of up to 30%. Regularly inspecting and replacing these tools can not only improve cutting precision but also extend the overall functionality of the CNC tube cutter. Furthermore, using the right coolant during operation is essential; inadequate lubrication can lead to overheating and ultimately damage the machine.
Additionally, software maintenance should not be overlooked. The integration of advanced software tools in CNC operations allows for precise machining and monitoring of machine conditions. Regular software updates can enhance performance and fix bugs that might hinder productivity. Reports suggest that facilities that invest in software training for operators see a 20% increase in overall equipment effectiveness (OEE). By following these maintenance tips, businesses can ensure their CNC tube cutters remain reliable and efficient over the long haul.
Distribution of CNC Tube Cutter Features
This pie chart illustrates the distribution of key features that industries consider when choosing a CNC tube cutter. Each segment represents the importance of specific features such as precision, speed, durability, ease of use, maintenance needs, and cost, helping buyers make informed decisions.