7 Reasons Why the Best CNC Plasma Table Revolutionizes Metal Fabrication Efficiency
In the rapidly evolving landscape of metal fabrication, the CNC plasma table has emerged as a game-changer, significantly enhancing efficiency and productivity. As we look ahead to the technological trends of 2025, it is essential to explore the profound impact that advanced CNC plasma tables are having on the industry. These sophisticated machines not only streamline the cutting process but also integrate seamlessly with design software, allowing for precise and automated workflows. This innovation is crucial for manufacturers aiming to meet rising demands while minimizing costs and reducing waste. In this blog, we will delve into seven compelling reasons why the best CNC plasma tables are revolutionizing metal fabrication and setting new standards for efficiency in the sector.
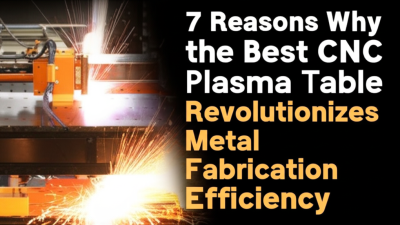
Key Features of High-Quality CNC Plasma Tables for Efficient Metal Fabrication
When it comes to enhancing metal fabrication efficiency, high-quality CNC plasma tables stand out as revolutionary tools. Their precision and speed significantly reduce production times while ensuring accuracy in cuts. One of the key features to look for in a CNC plasma table is its cutting speed, often measured in inches per minute. Tables that excel in this area can dramatically increase workflow, allowing fabricators to complete more projects in less time.
Another vital feature is the ability to integrate advanced software that allows for intricate design capabilities. This enables users to create complex shapes and profiles easily, transforming design ideas into reality with minimal effort. An essential tip for maximizing the efficiency of a CNC plasma table is to invest time in understanding the software and its functionalities. This knowledge can lead to better designs and faster production times.
Additionally, the construction quality of the table itself plays a crucial role in performance. A robust and sturdy frame minimizes vibration, which is paramount for maintaining precision during cutting operations. For optimal results, ensure that your CNC plasma table is equipped with reliable support systems and regular maintenance checks. Prioritizing these features will not only enhance your fabrication efficiency but also prolong the lifespan of your equipment.
7 Reasons Why the Best CNC Plasma Table Revolutionizes Metal Fabrication Efficiency
Identifying Reliable Suppliers for CNC Plasma Tables: What to Look For
When selecting a reliable supplier for CNC plasma tables, it's essential to consider several key factors that can significantly affect your metal fabrication efficiency. Industry reports indicate that the quality and precision of CNC equipment can improve operational efficiency by up to 25%, which emphasizes the importance of investing in the right machine. Suppliers that offer comprehensive warranties, customer support, and training can significantly enhance the user experience. According to the Fabricators & Manufacturers Association, businesses that receive adequate training on their equipment see productivity gains averaging around 20%.
Furthermore, it's crucial to assess the supplier's reputation in the market and their track record with previous customers. A recent survey by Modern Machine Shop highlighted that 67% of manufacturers prioritize supplier reputation and support services when choosing CNC equipment providers. Engaging with suppliers that have positive reviews and proven expertise in the CNC industry can provide a competitive edge in your fabrication processes. Overall, thorough research and consideration of these factors can lead to the selection of a supplier that not only meets your immediate needs but also contributes to long-term operational success.
The Impact of Advanced Technology on Metal Fabrication Efficiency
In the realm of metal fabrication, the advent of advanced technology, particularly CNC plasma tables, has significantly heightened efficiency and productivity. Reports indicate that companies utilizing CNC plasma cutting technology can increase their output by up to 25%, streamlining workflows and minimizing both material waste and labor costs. The ability of CNC plasma tables to carry out high-precision cuts quickly allows fabricators to meet tight deadlines and respond swiftly to market demands, ultimately enhancing competitive advantage.
Furthermore, a study by the Fabricators & Manufacturers Association International reveals that integrating CNC technology in metal fabrication processes has reduced operational costs by 15-20%. This is primarily due to lowered energy consumption and reduced manual labor. With capabilities that allow for intricate patterns and complex shapes, CNC plasma tables not only improve the quality of the finished product but also expand the design possibilities for engineers and designers. As the industry continues to embrace innovative technologies, the impact on efficiency is not just a trend but a transformative shift reshaping how metal fabrication is approached.
Comparative Analysis: In-House vs. Outsourced CNC Plasma Table Suppliers
When considering CNC plasma tables for metal fabrication, businesses often face the decision of whether to invest in in-house machinery or outsource to suppliers. Each approach has its benefits and drawbacks, and understanding these can greatly impact operational efficiency and cost-effectiveness. In-house CNC plasma tables provide companies with immediate access to high-quality cutting capabilities. They allow for greater control over production timelines, precision, and the opportunity for customizations based on specific project requirements. This direct oversight enables rapid responses to design changes or urgent orders, fostering innovation and adaptability in the manufacturing process.
On the other hand, outsourcing CNC plasma table services can relieve businesses of the considerable upfront costs and maintenance associated with owning and operating machinery. By partnering with specialized suppliers, companies can leverage advanced technologies without the burdens of equipment management. This approach often grants access to a wider range of cutting capabilities and expertise, maximizing productivity while minimizing overhead.
However, it's crucial for businesses to carefully evaluate potential suppliers, as the quality and reliability of their services can directly influence the overall efficiency of metal fabrication processes. Ultimately, the choice between in-house and outsourced CNC plasma table options should align with a company's specific needs and operational strategy.
Best Practices for Evaluating Customer Support from CNC Plasma Table Vendors
When investing in a CNC plasma table for metal fabrication, customer support can significantly influence your overall experience and efficiency. Before making a purchase, it's crucial to thoroughly evaluate vendor support services. Look for vendors that provide comprehensive resources, including online tutorials, user manuals, and troubleshooting guides. This support can greatly reduce downtime when you encounter issues or need to optimize your processes.
Another important aspect to consider is the responsiveness of the customer support team. A vendor that offers multi-channel support—such as phone, email, and live chat—can make a big difference when urgent questions arise. Ensure that the team is readily available and knowledgeable about their products. It's wise to ask about their average response times to gauge how effectively they can assist you during critical moments.
Lastly, consider the availability of on-site support or training. Some vendors offer installation assistance and training sessions, which can help you and your team become proficient with the new equipment. Ensuring that your CNC plasma table operates optimally from the start will enhance your production efficiency and overall success in metal fabrication.
7 Reasons Why the Best CNC Plasma Table Revolutionizes Metal Fabrication Efficiency - Best Practices for Evaluating Customer Support from CNC Plasma Table Vendors
Feature | Description | Impact on Efficiency | Vendor Support Rating (1-5) |
---|---|---|---|
High Cut Speed | Allows for faster processing of materials, reducing production time. | Increases output and overall productivity. | 4 |
Precision Cutting | Provides accurate cuts, minimizing material waste. | Enhances quality and reduces scrap costs. | 5 |
Software Integration | Easily integrates with existing CAD/CAM software. | Streamlines workflow and reduces design-to-production time. | 4 |
User-Friendly Interface | Intuitive controls that facilitate ease of use. | Minimizes training time and errors during operation. | 5 |
Durability | Constructed from high-quality materials for long lifespan. | Reduces downtime and maintenance costs. | 4 |
Remote Monitoring | Allows for real-time monitoring and troubleshooting remotely. | Increases responsiveness to issues and reduces downtime. | 5 |
Post-Purchase Support | Comprehensive training and ongoing technical support. | Ensures optimal use of the equipment post-purchase. | 5 |